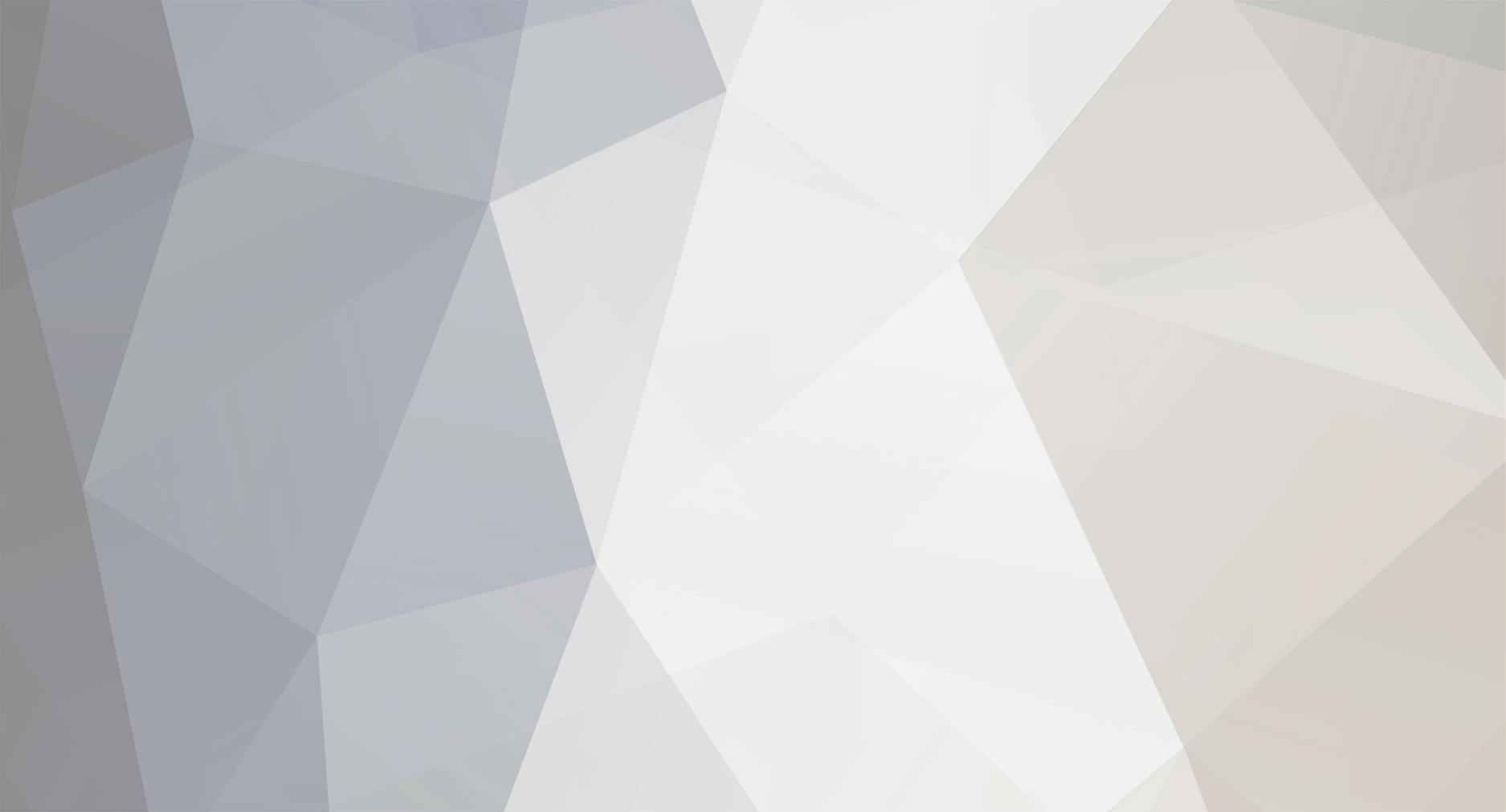
Lacessit
Advanced Member-
Posts
31,892 -
Joined
-
Last visited
-
Days Won
16
Content Type
Events
Forums
Downloads
Quizzes
Gallery
Blogs
Everything posted by Lacessit
-
If you need to ask that question, perhaps you are not one of them.
-
A tax loophole?
Lacessit replied to Lacessit's topic in Jobs, Economy, Banking, Business, Investments
Kerry Packer once famously said anyone who does not minimize their tax needs their head read. If I am bringing in AUD 5300 in savings to Thailand, please explain why that is income, and taxable. Also please explain how the Thai tax authorities can differentiate between income and savings in an Australian bank account. -
I am not aware of business class being available on domestic flights within Thailand. Normal people prefer to spend their money on things less ephemeral than business class big-noting.
- 139 replies
-
- 11
-
-
-
-
-
Very happy to be back here, I left Melbourne when it was 13 C, not counting windchill. Hoping to survive a plague carrier seated next to me, who coughed continuously from Melbourne to Singapore. The Singapore - Bangkok leg had a howling infant a few seats away. The joys of air travel.
-
I recently brought $5300 in cash { AUD } from Australia to Thailand, to be converted into baht when needed. It got me to thinking there is a way around the new personal tax regulations in Thailand, not that they are set in stone as yet. I have an Australian bank account, in which my age pension accumulates. I transfer by WISE every 4 - 6 months for living expenses. Those transfers may be taxed as they occur by Thai banks in the future, being classed as income. What if I had a trusted relative or friend who could send me cash by registered post instead, and I converted said cash to baht here? As I have said before, when governments make up stupid rules, people look for ways to circumvent them.
-
I guess everyone has seen people of all nationalities who are too cheap to purchase hold luggage, and instead have rigid suitcases which can barely fit into overhead lockers. If they all meet airline specifications for carry-on luggage, I will bare my bum in Times Square. Or the ones who have the carry-on, then add a couple of large Krispy Kreme boxes. Eat s##t and die. It's obvious the airlines do nothing to discourage the practice, even with items which are manifestly way over volume and weight restrictions. I am wondering when someone is going to be turned into a paraplegic by being hit with an oversize, overweight item tumbling onto their head from an overhead locker. And what excuses the airline will have. It also slows down the boarding and disembarkation processes, when most five foot Asians can't even reach the lip of the lockers. Being six foot, I used to help. Now I think, stew in your own juice.
- 139 replies
-
- 21
-
-
-
-
-
-
-
Trump trial: Publisher says he suppressed negative news
Lacessit replied to Social Media's topic in World News
This is only the first bar in the cage being erected around Trump by the prosecutors. If it was illegal to have affairs or employ hookers, there would be a lot more people in jail. The real meat is in where the hush money came from. -
-
You don't know what Schwab has invested your money in?
-
-
Non-Americans are quite bewildered by the bi-polar characteristics of the USA and its citizens. There are some things America is superbly competent at. In others, we can only gaze in wonder at abject stupidity.
-
I can ignore the occasional lapses from Biden, because I am old myself. I call them senior moments. IMO they don't matter, because Biden surrounded himself with able people. In contrast to Trump, who staffed the White House with toadies, and marginalized or got rid of anyone who dared disagree with him. Trump is probably right about the Washington swamp. When one in ten people in Washington is a lawyer, perhaps inevitable. However, all he did was replace the crocodiles with alligators.
-
"Beyond the confines of the courtroom, legal battles continued to unfold. A parallel hearing focused on allegations of Trump's violation of the judge's gag order, underscoring the contentious nature of the proceedings. Prosecutors sought sanctions against Trump for alleged breaches, highlighting the gravity of the situation. Meanwhile, Trump's legal team vehemently contested the allegations, setting the stage for a showdown over the boundaries of free speech and judicial oversight"
-
If you took the time to watch all of Biden's SOTU speech, you would maybe see someone who talks cogently and with vigor. Depending on how entrenched your bias is. Then tell me what you can detect in a Trump speech which remotely resembles a policy which will benefit the average American. After you have filtered out every deflection, non sequitur, and arrant nonsense.
-
How to retire in Thailand
Lacessit replied to CharlieH's topic in Thai Visas, Residency, and Work Permits
The video skates over several pertinent facts: 1/ Retirement has no permanency for foreigners in Thailand. At any time, on a whim of an IO, a visa extension may be refused. 2/ Foreigners have very few legal rights in Thailand. Thai courts will usually side with a Thai. 3/ It is still unclear whether the pensions of foreign retirees will be taxed by the Thai government, or whether everyone who resides in Thailand for more than 180 days per year needs a Thai tax number. 4/ Medical treatment can be extremely expensive. After more than 10 years in retirement here, 65% of my assets are still in my home country. Safer than burning all my bridges.- 222 replies
-
- 19
-
-
-
-
-
If one was to replace every ICE in Australia with an EV, it would reduce CO2 emissions by a mere 9%. EV's are good for city environments, by reducing air pollution. The simple fact is we are still reliant on fossil fuels for two-thirds of our electricity generation, EV's are a drop in the bucket in comparison.
-
What's a reasonable price for a lady drink?
Lacessit replied to TheFatOne's topic in ASEAN NOW Community Pub
How much do you think people pay for a wife? -
I had a partial denture done at Ram Hospital dental clinic in Chiang Mai many years ago. Still fits perfectly. An Australian dentist commented the denture was very good quality. Not cheap, IIRC 110,000 baht.
-
What's a reasonable price for a lady drink?
Lacessit replied to TheFatOne's topic in ASEAN NOW Community Pub
When I was in the bar scene years ago, 150 baht for a lady drink was about average. Usually the girl got 50 baht of that. Many lady drinks do not contain alcohol. Some girls don't want to be drunk all the time. Some girls also don't want to do P4P, they are content to make their money off the commissions. It's a transaction, they are giving you their time in exchange for your money. I never asked a girl to go with me. I waited for them to initiate discussion. -
My mistake - I have always thought the lyric was "the last train out of Sydney's almost gone".
-
Lots of Russians don't want to die in a meat grinder either, about 1 million have left Russia to avoid being drafted. I guess Putin's propaganda arm is not convincing them.
-
Normal people on this forum will be wondering whether your halo is strangling you.